Academia Member
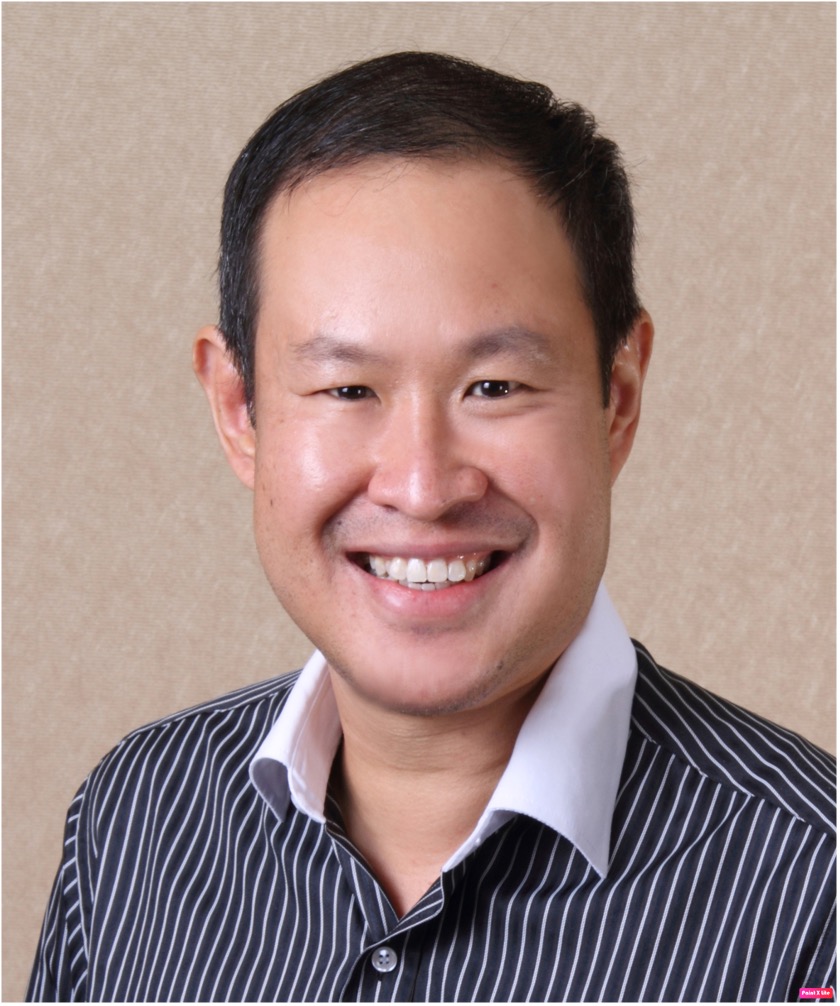
Alfred Tok
ALD artificial solid electrolyte interphase (SEI) for Li-battery
The applications of atomic layer deposition (ALD) technology in the Li-ion field are numerous: from protective coatings to high-surface area active materials and composite electrodes to manufacturing and production of battery materials. A brief depiction of LIBs component was first provided in Scheme 1 to help us to understand the advantages of ALD. A typical system is comprised of a cathode, which serves as the Li source in the system (usually a lithiated metal oxide), and an anode (most commonly graphitic carbonaceous materials). Both electrodes need to facilitate accommodation for Li storage inside their crystal structure. Between both electrodes an electrolyte serves as the conductive medium for Li-ion transport, while a separator is added in order to prevent shorts, control the diffusion rate, and inhibit Li dendrite formation and penetration that could cause a short circuit. Finally, current collectors on both sides provide the desired electron conductivity which promotes the flow of current through an external circuit.
In a typical discharge process, Li ions migrate out of the cathode and into the anode. In the case of graphite anode, e.g., Li ions accumulate and form a solid electrolyte interphase (SEI) around the outer surface of the anode, before penetrating between the graphitic layers, forming the LiC6 compound.2-3 The electrically insulating and ionically conductive SEI between anode and electrolyte is instantaneously formed by the parasitic reactions of Li metal and electrolyte in the initial cycles. The ideal SEI film can conscientiously protect Li metal with high stability and mechanical strength.4 . However, the as-formed SEI typically cannot withstand the drastic volume change induced by “hostless” Li metal, thus facilitating the formation of Li dendrites at cracks in the SEI layer and decay of Coulombic efficiencies.5 Hence, it is essential to build ultrathin, high Li-ion conductivity SEI with high stability and mechanical strength to inhibit the uncontrolled growth of Li dendrites and ensure a long cycling life with high Coulombic efficiency and good safety. ALD uses self-limiting chemical reactions between gaseous precursors and a solid surface to deposit materials in a layer-by-layer manner. This process results in a unique combination of attributes, including sub-nm precision, the capability to engineer surfaces and interfaces, and unparalleled conformality over high-aspect ratio and nanoporous structures. Given these capabilities, ALD could play an important role in achieving the technological advances in lithium-ion batteries (LIBs) research.
ALD has been carried out to synthesize and/or modify anodes, cathodes, and solid-state electrolytes for LIBs. One of the important applications of ALD is to provide a protective layer to the anode and cathode, since it can usually provide more uniform surface coverage than the conventional wet chemistry methods. The protective layer is able to improve the stability of the LIBs mainly by suppressing the side reaction between the electrolyte and electrodes, and therefore preventing the decomposition of electrolyte. Other benefits of adding a protective layer include (1) protecting the electrode from dissolving and (2) accommodating volume expansion during charge/discharge.
ALD-Modified Anodes
As the most well-established ALD process, Al2O3 deposition has been frequently used to generate protective layers for LIB anodes. An ultrathin 14 nm thick ALD Al2O3 layer to effectively prevent Li metal from corrosion of electrolyte.6 The thickness of the ALD Al2O3 layer can be even reduced to ∼2 nm, which can still prevent dendrite formation upon cycling at a current density of 1.0 mA cm–2.7 ALD Al2O3 can also function with other components to form a composite protective layer. Besides Al2O3, ALD transition metal oxides, such as TiO2,8-9 SnO2,10 HfO2,11 and SnO-TiO2 mixed oxide,12 were also studied as the passivation layer, and promising results were achieved. These thin oxide films prepared by ALD were used to protect a range of anode materials, such as carbon nanotubes (CNTs), graphene oxide (GO), carbon black, and silicon. For example, due to its capability of conformal coating on 3D framework, ALD has been employed to make an anode composed of SnO2@TiO2 double-shell nanotubes on carbon cloth.13 The hollow structure of the double-shell nanotubes accommodates the stress caused by the large volume expansion during battery cycling and has also been tested as a flexible anode for LIBs.
ALD-Modified cathodes
Similar with anode, metal oxide coatings have also been used to protect LIB cathode materials, and Al2O3 is the most common one. However, besides being unstable with HF, metal oxides also increase the impedance, which causes a noticeable deterioration of the battery high-rate performance. Metal fluoride coatings such as MgF2 and AlF3 have shown excellent stability during long-time cycling, but the lack of fluorine precursors makes the ALD process particularly challenging. the ALD of various metal fluorides has been demonstrated with new fluorine precursors other than HF. Lee et al. used an HF-pyridine complex as the fluorine precursor to grow MnF2, HfF4, MgF2, ZnF2, and ZrF4 films by ALD. The HF-pyridine complex is still based on HF, though much safer than the HF(g). Park et al. also deposited a highly conducting AlWxFy film on LiCoO2 by ALD, which enabled 99% capacity retention in cell tests after 50 cycles. Another promising aspect of ALD is the deposition of alloy protective layers on the electrodes. Laskar et al. reported that (Al2O3)1–x(Ga2O3)x alloy was coated on NCM by “co-pulsing” ALD.14 The “co-pulsing” ALD makes a more homogeneous gas phase flow to the surface than the sequential approach (Figure 2a). The Al/Ga ratio was varied to optimize the conductivity of the coating in which aluminum oxide is an insulator and gallium oxide is a semiconductor. High-resolution TEM image (Figure 2b) showed the amorphous nature of the AlGaoxide coating on crystalline NMC particle. If the protective layer is too conductive, the electric field within the layer will be too small to drive the Li ion to transport through the electrolyte. If the layer is too resistive, the internal resistance of the battery will be very high. The film with x = 0.5 and 2 ALD cycles showed the best rate performance (Figure 2c).
Solid-State-Electrolyte
ALD has offered a promising, alternative method to prepare all-solid-state thin film batteries due to its ability to coat the surface conformally. Several articles published before 2015 have reviewed the contribution of ALD in this area, particularly preparing solid electrolyte interphase as a protecting layer.[1,82 Many materials have synthesized using ALD, such as LiAlSiO4, Li2O-Al2O3, Li3PO4, etc. The presence of these solid electrolyte thin films either as part of the all-solid-electrolyte LIBs or protecting layer of anode metal or cathodes, indeed increases the cycling performance and stability. However, using ALD to synthesize lithium-containing solid electrolyte also faces challenges. In almost all the cases, lithium tert-butoxide were chosen as the lithium precursor. This precursor needs relative high heating temperature (≈140 °C) to maintain a feasible partial pressure, which may limit its low temperature application such as deposition on conductive polymers and metal-organicframeworks (MOFs). Other options of lithium precursors are desired for such applications. In addition, the synthesis of solid-stateelectrolyte using thermal ALD requires very high temperature (≈300 °C). Otherwise, a plasma source is required to break down molecules at lower temperature, particularly for the synthesis of LiPON. With the use of a plasma source, it is questionable whether conformal coating can be truly achieved on high-aspectratio substrates. For this reason, solid-state-electrolytes synthesized by ALD have been mostly demonstrated on planar surfaces. Elam and co-workers developed a strategy to synthesize LixAlyS solidstate electrolyte on copper surface at as low as 150 °C using thermal ALD.16 With the use of thermal ALD, it is promising that this material can be also applied on high surface area substrates in the future to achieve even better electrochemical properties. Recently, Philippe and co-workers reported on the first thin-film solid nanocomposite electrolyte (NCE) for lithium-ion batteries made by combining two gas-phase deposition techniques, molecular layer deposition (MLD) and atomic layer deposition (ALD). The advantage of using these techniques for the fabrication of NCEs comes from the ease of integration in thin-film batteries and the possibility to alter the properties of the oxide matrix and of the Li-compound independently.17
The application of the ALD technique has dramatically improved the cycle life and high-rate performance of LIBs, but all issues are not completely resolved. As mentioned earlier, protecting the electrode materials from attack by the byproduct HF is still challenging. Thus, the ALD coating should not be limited in the common metal oxides, e.g., Al2O3 and TiO2, especially when the instability of the metal oxides is known. Discovering new and effective ALD coating materials, especially appropriate precursors, is challenging and urgent. The mechanism of the interaction of the ALD-coated electrode and solid-state electrolyte materials needs more study. Up to now, most of the reported work focuses on the performance of the battery rather than the interaction between the ALD materials with the other components of the battery during charge/discharge. The mechanism studies will provide a deeper understanding on the function of these ALD materials, which will contribute to the rational design of the electrode, electrolyte, and even the whole LIBs.